Знос інструментів при землерийних роботах
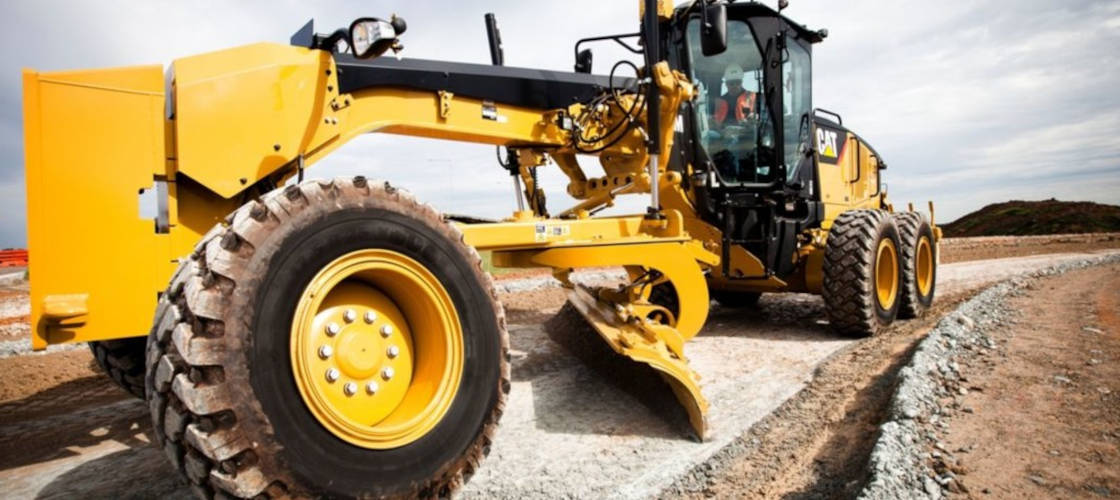
Близько 80% від загального числа поломок спецтехніки викликані зносом деталей. Особливо інтенсивно абразивному зношуванню піддаються робочі органи землерийних машин - наконечники розпушувачів, зубці ковшів екскаваторів та навантажувачів, різці дорожніх фрез, а також ножі грейдерів і бульдозерів.
Природа зносу інструменту землерийних машин
Робочі органи землерийних машин служать для відділення ґрунту від масиву, зміщення його до місця відвалу або до місця навантаження в транспортний засіб. Всі роботи, які виконують робочі органи землерийних машин, можна розділити на 3 види: підготовчі, основні, оздоблювальні.
Підготовчі роботи включають зняття поверхневого шару ґрунту за допомогою відвалів або інструментів ковшового типу. Основні роботи полягають в розробці кар'єрів, виїмок, котлованів, траншей. Такі роботи виконуються екскаваторами й інструментами землерийно-транспортних машин, таких як бульдозери, скрепери, грейдери-елеватори тощо. До оздоблювальних робіт відносять різного роду планування насипів, каналів, нарізку кюветів. Всі планувальні операції виконуються робочими органами автогрейдерів, одно- чи багатоковшовими планувальниками.

Матеріали та конструкції інструментів підбираються при експлуатації відповідно до фізико-механічних властивостей порід і ґрунтів, з якими доводиться працювати. Основними мінералами, що визначають властивості ґрунту, є польовий шпат, слюда, кварц та інші. Кварц (SiO2), головний мінерал в складі пісків і суглинків, має твердість по Брінеллю 800-1200 кг/мм², в той час як твердість металу, з якого виготовлені землерийні органи, у багатьох випадках не перевищує 350-400 кг/мм².
Природно, з огляду на таку різницю в твердості, зубці, передні стінки ковшів, ножі бульдозерів і автогрейдерів та інші деталі робочих органів піддаються інтенсивному зношуванню. Швидкість зносу оцінюється приблизно в 5-400 мкм/год. Для більш наочного уявлення про швидкість зношування - товщина людської волосини, в середньому, становить 40 мкм.
Основна маса землерийних машин використовує при роботі принцип різання ґрунту. Головне навантаження на робочі органи та машину в цілому виникає в результаті дії сил комплексного опору копанню, причому основну частину сили копання становить сила різання. Наприклад, при роботі бульдозера 60-85% сили копання доводиться на силу різання, екскаватор витрачає взагалі 74% від витрачених сил копання на різання.
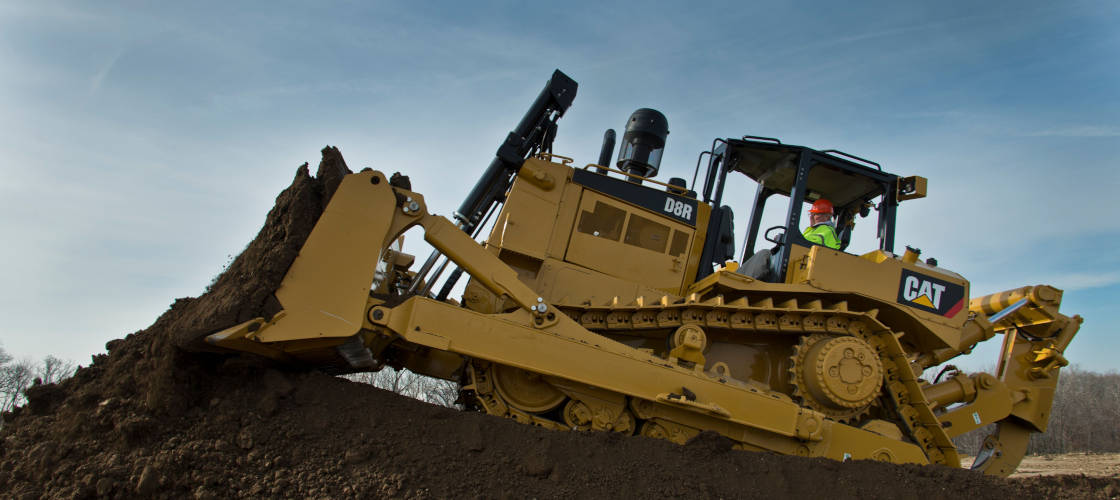
Якщо розглянути процес різання трохи докладніше, то він виглядає наступним чином: в першу чергу, виникає контакт і вдавлення клина робочого інструмента в ґрунт. Після впровадження твердосплавного клина в місці контакту утворюється шар, який називають «ядро ущільнення». По мірі зростання зусилля різання відбувається відкол великого шматка ґрунту. У цей момент раніше важко навантажений клин різко звільняється від навантаження, але одразу відбувається удар об наступний масив ґрунту. В результаті, такий процес можна охарактеризувати як чергування піків ударного навантаження з періодами статичного навантаження. У процесі різання мають місце і удари інструменту з прослизанням, хоча цей процес більше характерний при розробках кускових порід.
Про знос ножів
Основним елементом бульдозерного обладнання є відвал. Найбільш затребувані - універсальні відвали, в яких передбачено зміну поперечних і поздовжніх кутів установки, кріпляться вони шарнірно до П-подібної штовхаючої рами. На другому місці за поширеністю - скельні відвали, вони меншої ширини та ємності, бо скельний ґрунт має велику питому вагу, проте ці відвали відрізняються посиленою конструкцією. Перед тим, як вибрати відвал, необхідно оцінити міцність ґрунту в місці робіт, тягово-зчіпні і швидкісні характеристики бульдозера. Чим вище значення відношення тягового зусилля до довжини ножа, тим міцніші ґрунти такому бульдозеру «по плечу».
У нижній частині лобового листа відвала закріплений, як правило, з'ємний складовий ніж товщиною 10 мм і більше. Він складається із середньої частини, розділеної на 2 або 3 середніх ножі, є також 2 коротких бічних ножа. Вони розташовані з боків від середнього ножа. Така конструкція збільшує ремонтопридатність і полегшує монтаж. Середні ножі - 2-сторонні. При зносі гострої кромки одного боку для подальшої експлуатації ніж розгортають на 180 градусів. Бічні ножі односторонні, але для підвищення зносостійкості мають більшу товщину, ніж середні.
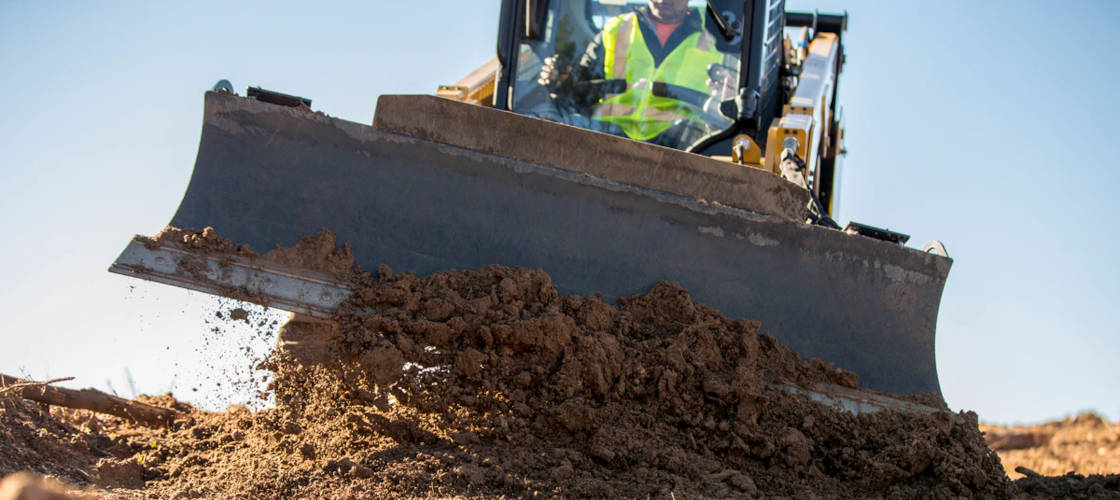
Ножі землерийних машин завжди до певної міри затуплені. Їх форма і лінійні розміри піддаються абразивному впливу ґрунтів і в процесі експлуатації змінюються, тобто зношуються. Бульдозерні ножі зношуються по своїй ріжучій кромці. Основними ознаками зношення є глибокі подряпини та борозни різної глибини. Для бульдозерів характерна тривалість використання комплекту ножів при розробці ґрунту 240-720 годин.
Ножі автогрейдерів, так само як і ножі бульдозерів, зношуються по всій ріжучій кромці, працюючи до остаточного зносу, тобто з двох сторін, 80-400 годин. За товщиною зазвичай зношення ножа незначне, тому зміна цього параметра практично не враховується.
Такий широкий діапазон ресурсу ножів пов'язаний з абразивністю розроблюваних ґрунтів. Довговічність роботи ножів визначається по зносу ширини. Спочатку ширина ножа становить близько 45-55 мм при куті різання 35 градусів. «Майданчик зносу» такого ножа - близько 17 мм, але оскільки зі збільшенням зносу відбувається різке зростання навантаження, граничною величиною зносу для ножів автогрейдерів прийнято вважати 10-12 мм.
Відносно короткий період використання робочого органу безпосередньо пов'язаний з величезним збільшенням сили різання при роботі зношеними ножами. При просуванні в ґрунті, крім опору від руху своєї передньої частини, зношений ніж долає опір майданчика зносу, що має невеликий негативний кут щодо основної траєкторії різання.
Ще одним видом зносу ножа ріжучого інструменту є затуплення, що також істотно підвищує опір ґрунту. При різанні затупленим інструментом характерне утворення на тупій поверхні ґрунтового наросту, який збільшує тіло ножа і, так само як і основний ніж, бере участь в різанні ґрунту. Таке потовщення значно підвищує силу різання.
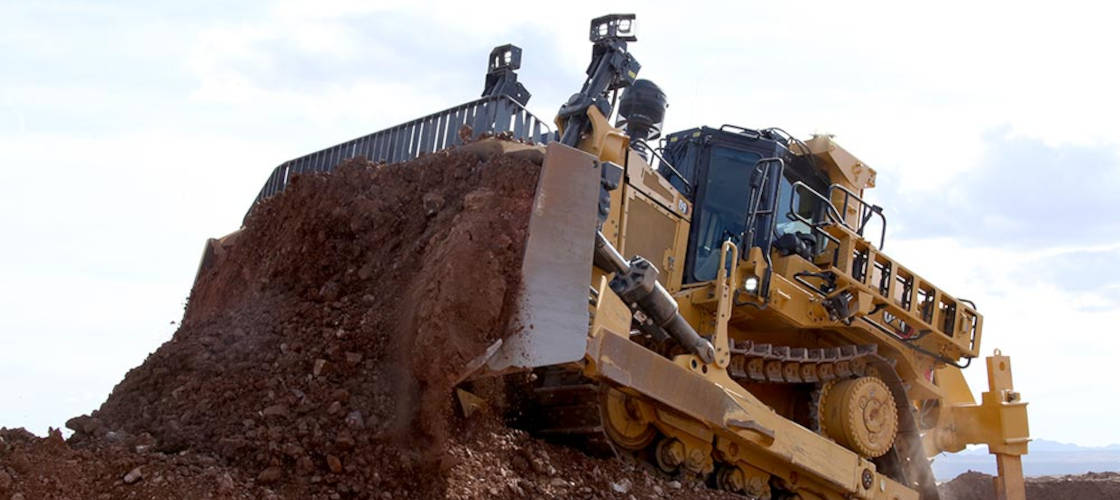
Треба відзначити, що знос ножів не рівномірний. Поблизу ріжучої кромки поверхня ножа контактує з частинками ґрунту, які ще є частиною ґрунтового масиву. Вони діють на ніж як різці, інтенсивно зношуючи його кромку. По мірі віддалення від ріжучої кромки збільшуються деформації і напруги в ґрунті, частинки ґрунту стають рухливими, втрачаючи структурні зв'язки між собою. Їх переміщення по поверхні різця можна визначити як перекочування, що, звичайно, зменшує абразивну дію на площину різця, однак тиск на ґрунт зростає.
На інтенсивність зносу робочих органів дорожньо-будівельних машин, безумовно, великий вплив мають фізико-механічні властивості ґрунту, що розробляється. Мають значення його зчеплення, внутрішнє і зовнішнє тертя, різним видам ґрунтів відповідає різний показник питомого опору різання.
Ремонт наплавленням
Найбільш поширений та ефективний метод ремонту робочих органів - це наплавка зношених місць зносостійкими сплавами.
Бульдозерні ножі при технічному обслуговуванні оглядають, відзначають фарбою всі дефекти, які необхідно усунути, при необхідності демонтують і рихтують під пресом, адже при середній довжині ножа 2,5-3,5 м допускається рельєфність не вище 3 мм на 1 м довжини ножа, погнутості та вм'ятини не допускаються. Ножі наплавляють ручним зварюванням у місцях найбільшого зносу. Для нових ножів також іноді здійснюють наплавлення в профілактичних цілях.
Для того щоб не відбувалося викривлення, ніж закріплюється в спеціальному пристрої і наплавка здійснюється ділянками, по черзі з однієї та іншої сторони. Товщина наплавочного шару - 3-5 мм, а ширина смуги - 60 мм.
Перед наплавленням деталь очищають від бруду, мастила, іржі тощо, потім зачищають до чистого металу. Якщо виявляють тріщини і злами, деталь бракується остаточно.
При ремонті зубців екскаваторів їх можуть наплавити прямо на ковші або демонтувавши його. В останньому випадку ківш поміщають на спеціальний стенд, а зубці, як відновлювані, так і нові, що встановлюються замість вилучених, - в спеціальні кондуктори, які забезпечують горизонтальне положення площин наплавки.
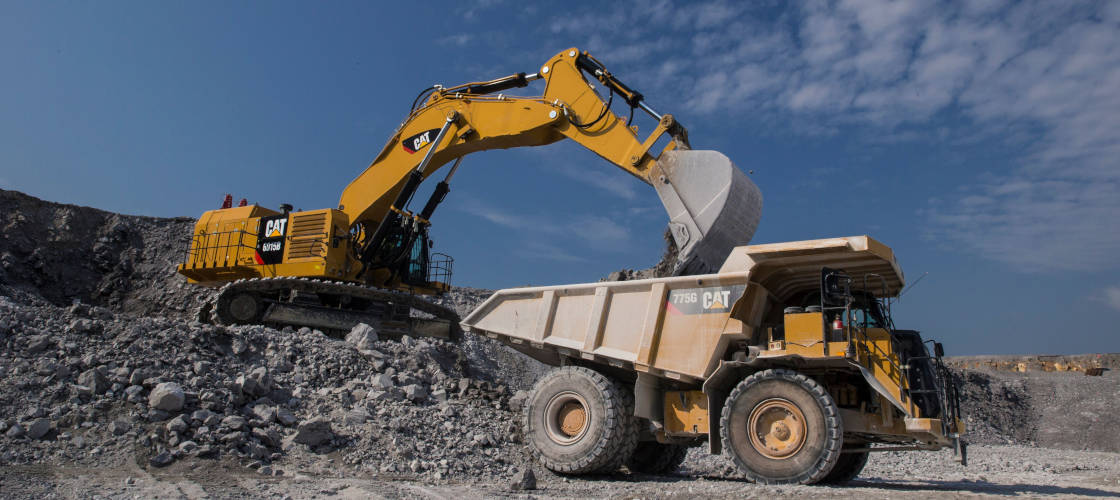
На підставі аналізу навантажень, що викликають підвищений знос зубців, визначають форму наплавлення. При незначних динамічних навантаженнях наплавляють тільки верхню межу зубця. Якщо ж очікується, що зубці будуть працювати в умовах високого динамічного навантаження, то здійснюють так звану корончату наплавку.
Самі ковші також наплавляють, як і зубці. За допомогою наплавлення зміцнюють ділянки між зубцями та бічні заокруглення передньої стінки. При необхідності наплавляють і інші ділянки. Причому, якщо зношування спостерігається сильне, то ківш наплавляють суцільним швом, а якщо незначне - застосовують сітчасту наплавку (наплавка відбувається ділянками, а відстань між ділянками наплавлення - це одна або дві ширини наплавленої ділянки). Форма наплавлення в цьому випадку - корончата. Товщина наплавленого шару складає 4-5 мм, а ширина смужки в малих ковшах з об'ємом менше 0,35 м3 - приблизно 40 мм, а в ковшах з об'ємом понад 0,65 м³ - до 160 мм.
Один з лідерів у виробництві спецтехніки, компанія Caterpillar, використовує ножі з легованої сталі. Вводячи до складу сталі такі елементи, як нікель або бор, для ударної стійкості та високої зносостійкості.