Практичні поради для правильної експлуатації гідромолота
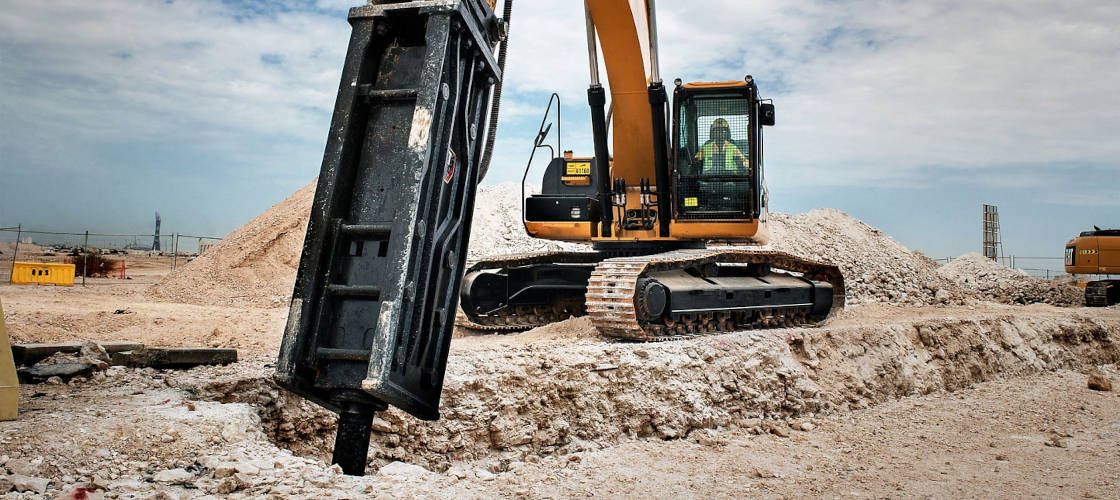
Щоб продовжити термін служби змінного інструменту, гідромолот слід встановлювати на об'єкт, що руйнується, так, щоб його поздовжня вісь була перпендикулярна поверхні руйнування: в цьому випадку знижується ймовірність зісковзування інструменту і зменшуються радіальні навантаження на інструмент, що виникають при ударі. Великі радіальні навантаження призводять до швидкого зносу напрямних втулок гідромолота і самого інструменту, а в екстремальних випадках можуть призвести до поломки інструменту під дією великого згинального моменту.
Якщо оброблюваний матеріал не руйнується під дією гідромолота протягом 15 - 30 секунд, то слід переставити молот на іншу точку, ближче до краю, тобто ближче до вільної поверхні. Така перестановка необхідна не тільки для досягнення більшої продуктивності, але і для забезпечення безпеки змінного інструменту гідромолота. При тривалій безперервній роботі на одній точці гострий кінець інструменту може розжаритися, що призведе до відпуску загартованого металу. В цьому випадку вістря інструменту втрачає свою твердість і швидко зношується або втрачає форму, розплющується. При заклинюванні робочого інструмента в оброблюваному матеріалі не треба намагатися звільнити його різкими рухами робочого обладнання або ходом екскаватора - це може привести до поломки інструменту.
При роботі молота хвостовик інструмента переміщується в направляючих втулках. Оскільки практично неможливо притискати молот точно по поздовжній осі, хвостовик інструмента відчуває вплив досить великої сили тертя. Крім того, в зазор між інструментом і втулками неминуче потрапляють абразивні частинки пилу від матеріалу, що руйнується. Інструмент і втулки відносяться до компонентів, які швидко зношуються, тому для продовження терміну служби ця пара завжди повинна бути покрита мастилом.
- Практика показує, що поновлювати мастило треба через кожні 2 - 3 години роботи молота, а при роботах у сильно запилених місцях частіше. Для досягнення найкращих результатів слід застосовувати консистентні мастила, що містять графіт або дісульфіт молібдену.
В процесі експлуатації гідромолота необхідно регулярно перевіряти величину зазору між хвостовиком інструменту і втулкою. Часто можна спостерігати, що інструмент вільно бовтається у втулці. Це є сигналом для заміни не тільки інструменту, але і втулок. Гранично допустимий знос пари інструмент-втулка залежить від величини посадкового діаметра хвостовика інструменту. Деякі зарубіжні фірми рекомендують наступні максимально допустимі діаметральні зазори:
Посадковий діаметр інструмента, мм | 50 - 100 | 100 - 135 | 140 - 160 | 170 - 215 |
Максимально допустимий зазор, мм | 4 | 6 | 8 | 10 |
Таким чином, допустимий зазор в парі інструмент-втулка, що виникає внаслідок зносу, не повинен перевищувати приблизно 5 - 6% від величини номінального посадкового діаметра інструмента.
При притисканні гідромолота до матеріалу, що обробляється, інструмент через наявність зазору відхиляється в сторону від осі гідромолота і його вісь перехрещується з віссю бойка. Чим більший кут між цими осями, тим більша радіальна складова сили, що виникає при ударі. Тому при великих зазорах на інструмент діють великі згинальні моменти, що збільшує швидкість зносу і в підсумку призводить до пошкодження інструменту: він або викривляється, або руйнується.
Забиваючи інструмент в ґрунт, не слід намагатися “виламати” шматок матеріалу, що руйнується, зусиллями гідроциліндрів робочого обладнання екскаватора. При такому способі роботи ймовірність поломки інструменту дуже висока. Якщо при цьому гідромолот продовжує працювати, а втулки інструменту зношені, то поломка інструменту майже гарантована.
Робота гідромолота зі зношеними втулками небезпечна і тим, що бойок молота завдає удари по краю торця інструменту. При цьому починають фарбуватися краї торців інструменту та бойка. Частки металу, що відкололися, потрапляють між торцями бойка і інструменту, що прискорює подальше руйнування. У деяких моделях гідромолотів верхній торець змінних інструментів виконаний у вигляді сфери, центр якої знаходиться приблизно в середині опорної поверхні втулок. В цьому випадку при повороті інструменту в межах зазору між втулками точка контакту бойка з інструментом мало відхиляється від центру, навантаження діють по осі бойка та інструменту, що знижує ймовірність їх пошкодження. Однак при будь-якій конструкції інструменту необхідно стежити за величиною зносу втулок і своєчасно їх замінювати.
Як провести діагностику гідромолота?
Спочатку гідромолоти розбирають по деталях і проводять їх візуальний огляд, потім визначається категорія складності ремонту і з'ясовуються причини поломки.
Які бувають причини для ремонту гідромолота і як усунути поломку?
Проблема в центральній частині ударного блоку - циліндрі, на якому утворилися зачіпки.
Для їх усунення необхідні шліфування та азотування деталі. На основі нового діаметра циліндра виготовляється бойок ремонтного розміру, що забезпечує необхідний зазор між дзеркалом робочого циліндра і поршневою частиною бойка. Від справної роботи бойка залежить тривалість життєвого циклу всього обладнання.
Для повного відновлення гідромолотів може знадобитися заміна стяжних шпильок з гайками, нижньої і верхньої втулок робочого інструмента, упорного кільця, пальців, ущільнень ремонтного розміру під поршень і робочих інструментів - пік.
Як запобігти ремонту гідромолота?
Щоб гідромолот працював без поломок і простоїв, досить дотримуватися простих правил його експлуатації:
- обов'язково налаштуйте параметри гідролінії на базовій машині під гідромолот. Зробіть це знову, якщо обладнання повернулося після ремонту
- обов'язково ознайомте оператора з правилами експлуатації обладнання
- дотримуйтесь правил зберігання гідромолота - в вертикальному положенні, азот в пневмокамері повністю спущений, в приміщенні температура не менше 10 ° С
- після кожних 50 мотогодин роботи перевіряйте всі з'єднання гідромолота.
Не забувайте змащувати робочий інструмент після кожних трьох годин експлуатації (при автоматичному змащуванні вчасно замінюйте картридж).